1. 밀링 커터의 선택 과정은 일반적으로 다음과 같은 측면을 고려하여 선택합니다.
(1) 부품 모양(가공 프로파일 고려): 가공 프로파일은 일반적으로 평면, 깊은, 공동, 나사산 등일 수 있습니다. 다양한 가공 프로파일에 사용되는 도구는 다릅니다. 예를 들어, 필렛 밀링 커터는 볼록한 표면을 밀링할 수 있지만 오목한 표면을 밀링할 수는 없습니다.
(2) 재질 : 가공성, 칩 형성성, 경도 및 합금 원소를 고려하십시오. 공구 제조업체는 일반적으로 재료를 강철, 스테인레스강, 주철, 비철금속, 초합금, 티타늄 합금 및 경질 재료로 분류합니다.
(3) 가공 조건 : 가공 조건에는 공작 기계 고정 장치의 공작물 시스템 안정성, 공구 홀더의 클램핑 상황 등이 포함됩니다.
(4) 공작기계-치구-가공물 시스템 안정성: 이를 위해서는 공작기계의 가용 출력, 스핀들 유형 및 사양, 공작기계의 연식 등, 공구 홀더의 긴 오버행과 축/ 방사형 런아웃 상황.
(5) 가공 카테고리 및 하위 카테고리: 숄더 밀링, 평면 밀링, 프로파일 밀링 등이 포함되며 공구 선택을 위해 공구의 특성과 결합되어야 합니다.
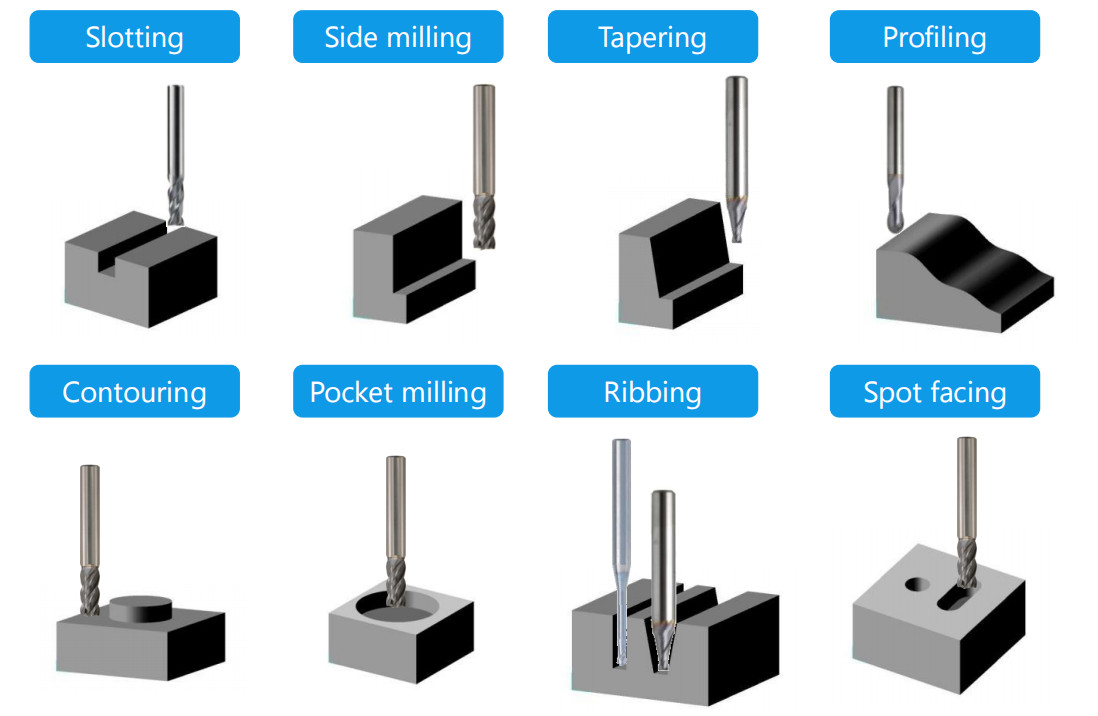
2. 밀링 커터의 기하학적 각도 선택
(1) 정면 각도의 선택. 밀링 커터의 경사각은 공구 및 공작물의 재질에 따라 결정되어야 합니다. 밀링 가공 시 충격이 가해지는 경우가 많기 때문에 절삭날의 강도를 높이는 것이 필요합니다. 일반적으로 밀링 커터의 경사각은 선삭 공구의 절삭 경사각보다 작습니다. 고속도강은 초경합금 공구보다 큽니다. 또한 플라스틱 재료를 밀링할 때 절단 변형이 크기 때문에 더 큰 경사각을 사용해야 합니다. 부서지기 쉬운 재료를 밀링할 때 경사각은 더 작아야 합니다. 강도와 경도가 높은 재료를 가공할 때는 음의 경사각을 사용할 수도 있습니다.
(2) 블레이드 경사 선택. 엔드밀의 바깥쪽 원과 원통형 밀링 커터의 나선각 β는 블레이드 경사 λs입니다. 이를 통해 커터 톱니가 공작물을 점진적으로 절삭 및 절삭할 수 있어 밀링의 매끄러움이 향상됩니다. β를 높이면 실제 경사각이 커지고 절삭날이 날카로워지며 칩 배출이 쉬워집니다. 밀링 폭이 좁은 밀링 커터의 경우 나선 각도 β를 늘리는 것은 거의 중요하지 않으므로 일반적으로 β=0 또는 더 작은 값이 사용됩니다.
(3) 주 편향 각도와 보조 편향 각도의 선택. 평면 밀링 커터의 절입각 효과와 밀링 공정에 미치는 영향은 선삭 시 선삭 공구의 절입각과 동일합니다. 일반적으로 사용되는 절입각은 45°, 60°, 75°, 90°입니다. 프로세스 시스템의 강성은 좋으며 더 작은 값이 사용됩니다. 그렇지 않으면 더 큰 값이 사용되며 절입각 선택은 표 4-3에 나와 있습니다. 2차 편향각은 일반적으로 5°~10°입니다. 원통형 밀링 커터에는 주 절삭날만 있고 보조 절삭날이 없으므로 보조 편향각이 없고 절입각은 90°입니다.
게시 시간: 2018년 4월 17일