응고 중 가스 포획으로 인해 형성되는 공동 형태의 불연속성인 다공성은 MIG 용접에서 일반적이지만 성가신 결함이며 여러 가지 원인이 있습니다. 이는 반자동 또는 로봇 응용 분야에서 나타날 수 있으며 두 경우 모두 제거 및 재작업이 필요하므로 가동 중지 시간이 발생하고 비용이 증가합니다.
철강 용접에서 기공이 발생하는 주요 원인은 용접 풀에 관여하는 질소(N2)입니다. 액체 풀이 냉각되면 N2의 용해도가 크게 감소하고 N2가 용강 밖으로 빠져나와 기포(기공)를 형성합니다. 아연도금/아연도금 용접에서는 증발된 아연이 용접 풀 내로 휘저어질 수 있으며, 풀이 응고되기 전에 빠져나갈 시간이 충분하지 않으면 기공이 형성됩니다. 알루미늄 용접의 경우 모든 다공성은 강철에서 N2가 작용하는 것과 마찬가지로 수소(H2)로 인해 발생합니다.
용접 다공성은 외부 또는 내부에 나타날 수 있습니다(종종 표면 아래 다공성이라고 함). 또한 용접의 한 지점이나 전체 길이에 걸쳐 발생하여 용접이 약해질 수도 있습니다.
다공성의 주요 원인을 식별하는 방법과 이를 신속하게 해결하는 방법을 알면 품질, 생산성 및 수익을 개선하는 데 도움이 될 수 있습니다.
열악한 차폐 가스 적용 범위
열악한 보호 가스 적용 범위는 대기 가스(N2 및 H2)가 용접 풀을 오염시킬 수 있기 때문에 용접 다공성의 가장 일반적인 원인입니다. 적절한 커버리지 부족은 차폐 가스 유량 저하, 가스 채널의 누출, 용접 셀의 공기 흐름 과다 등을 포함하되 이에 국한되지 않는 여러 가지 이유로 발생할 수 있습니다. 너무 빠른 이동 속도도 원인이 될 수 있습니다.
작업자가 불량한 흐름이 문제의 원인이라고 의심하는 경우 가스 유량계를 조정하여 속도가 적절한지 확인하십시오. 예를 들어 스프레이 전달 모드를 사용하는 경우 시간당 35~50입방피트(cfh)의 유량이면 충분합니다. 더 높은 암페어에서 용접하려면 유량을 늘려야 하지만 유량을 너무 높게 설정하지 않는 것이 중요합니다. 이로 인해 일부 총 설계에서 보호 가스 적용 범위를 방해하는 난류가 발생할 수 있습니다.
다르게 설계된 건은 가스 흐름 특성도 다르다는 점에 유의하는 것이 중요합니다(아래 두 가지 예 참조). 상단 디자인의 가스 유량의 "최적 지점"은 하단 디자인의 가스 유량보다 훨씬 큽니다. 이는 용접 엔지니어가 용접 셀을 설정할 때 고려해야 할 사항입니다.
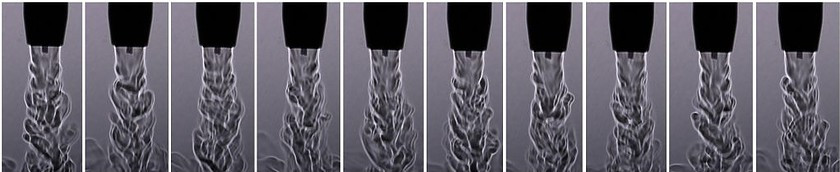
디자인 1은 노즐 출구에서의 원활한 가스 흐름을 보여줍니다.
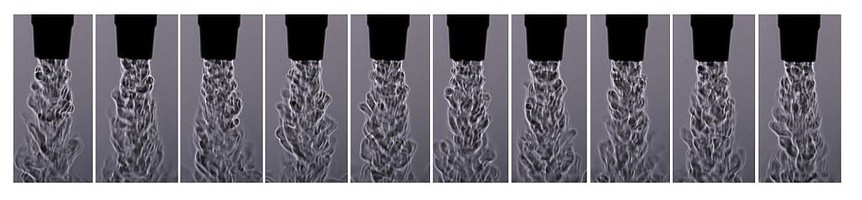
디자인 2는 노즐 출구에서의 난류 가스 흐름을 보여줍니다.
또한 MIG 용접건의 전원 핀에 있는 O-링뿐만 아니라 가스 호스, 피팅, 커넥터의 손상도 확인하십시오. 필요에 따라 교체하십시오.
팬을 사용하여 작업자나 용접 셀의 부품을 냉각할 때 팬이 가스 커버리지를 방해할 수 있는 용접 영역을 직접 향하지 않도록 주의하십시오. 외부 공기 흐름으로부터 보호하기 위해 용접 셀에 스크린을 놓습니다.
로봇 응용 프로그램에서 프로그램을 다시 터치하여 원하는 호 길이에 따라 일반적으로 ½ ~ 3/4인치인 적절한 팁-작업 거리가 있는지 확인합니다.
마지막으로 다공성이 지속되면 이동 속도를 낮추거나 더 나은 가스 적용 범위를 갖춘 다양한 프런트엔드 구성 요소에 대해 MIG 건 공급업체에 문의하세요.
비금속 오염
비금속 오염은 오일 및 그리스부터 흑피 및 녹에 이르기까지 다공성이 발생하는 또 다른 이유입니다. 습기는 특히 알루미늄 용접에서 이러한 불연속성을 조장할 수도 있습니다. 이러한 유형의 오염 물질은 일반적으로 작업자가 볼 수 있는 외부 다공성을 유발합니다. 아연도금 강철은 지하에 다공성이 발생하기 쉽습니다.
외부 기공을 방지하려면 용접 전에 모재를 철저히 청소하고 금속 코어 용접 와이어 사용을 고려하십시오. 이 유형의 와이어는 단선보다 탈산제 함량이 높기 때문에 모재에 남아 있는 오염 물질에 대한 내성이 더 높습니다. 항상 식물과 비슷하거나 약간 높은 온도의 건조하고 깨끗한 장소에 이러한 전선과 기타 전선을 보관하십시오. 이렇게 하면 용접 풀에 습기가 유입되어 다공성을 유발할 수 있는 응결을 최소화하는 데 도움이 됩니다. 전선을 추운 창고나 옥외에 보관하지 마십시오.
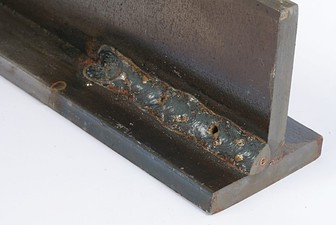
응고 중 가스 포획으로 인해 형성되는 공동 형태의 불연속성인 다공성은 MIG 용접에서 일반적이지만 성가신 결함이며 여러 가지 원인이 있습니다.
아연 도금 강철을 용접할 때 강철이 녹는 온도보다 낮은 온도에서 아연이 기화하며, 이동 속도가 빠르면 용접 풀이 빨리 얼어붙는 경향이 있습니다. 이로 인해 강철에 아연 증기가 갇히게 되어 다공성이 발생할 수 있습니다. 이동 속도를 모니터링하여 이러한 상황을 해결하세요. 이번에도 용접 풀에서 아연 증기가 빠져나가는 것을 촉진하는 특별히 설계된(플럭스 공식) 금속 코어 와이어를 고려하십시오.
막혔거나 크기가 작은 노즐
막히거나 크기가 작은 노즐도 다공성을 유발할 수 있습니다. 용접 스패터는 노즐과 접촉 팁 및 디퓨저 표면에 쌓여 차폐 가스 흐름을 제한하거나 난류를 일으킬 수 있습니다. 두 상황 모두 용접 풀에 부적절한 보호를 제공합니다.
이러한 상황을 더욱 복잡하게 만드는 것은 노즐이 해당 용도에 비해 너무 작고 더 크고 빠르게 스패터가 쌓이는 경향이 있다는 것입니다. 노즐이 작을수록 조인트 접근이 더 좋아지지만 가스 흐름에 허용되는 단면적이 작아 가스 흐름을 방해할 수도 있습니다. 노즐 돌출(또는 함몰)에 대한 접촉 팁의 변수를 항상 염두에 두십시오. 이는 노즐 선택 시 차폐 가스 흐름과 다공성에 영향을 미치는 또 다른 요소일 수 있기 때문입니다.
이를 염두에 두고 노즐이 용도에 맞게 충분히 큰지 확인하십시오. 일반적으로 더 큰 와이어 크기를 사용하는 높은 용접 전류를 적용하려면 더 큰 보어 크기의 노즐이 필요합니다.
반자동 용접에서는 노즐의 용접 스패터를 주기적으로 점검하고 용접기(웰퍼)를 사용하여 제거하거나 필요한 경우 노즐을 교체하십시오. 이 검사 중에 접촉 팁의 모양이 양호하고 가스 디퓨저에 깨끗한 가스 포트가 있는지 확인하십시오. 작업자는 스패터 방지 화합물을 사용할 수도 있지만 노즐을 화합물에 너무 멀리 또는 너무 오랫동안 담그지 않도록 주의해야 합니다. 과도한 양의 화합물이 보호 가스를 오염시키고 노즐 절연체를 손상시킬 수 있기 때문입니다.
로봇 용접 작업에서는 스패터 축적을 방지하기 위해 노즐 청소 스테이션이나 리머에 투자하십시오. 이 주변 장치는 생산이 중단되는 동안 노즐과 디퓨저를 청소하므로 사이클 시간에 영향을 주지 않습니다. 노즐 청소 스테이션은 전면 구성 요소에 화합물의 얇은 코팅을 적용하는 스패터 방지 스프레이와 함께 작동하도록 고안되었습니다. 스패터 방지액이 너무 많거나 너무 적으면 다공성이 증가할 수 있습니다. 노즐 청소 과정에 공기 분사 장치를 추가하면 소모품에서 떨어져 나온 튀김을 제거하는 데 도움이 될 수도 있습니다.
품질과 생산성 유지
용접 공정을 주의 깊게 모니터링하고 다공성의 원인을 파악하면 솔루션을 구현하는 것이 상대적으로 간단합니다. 그렇게 하면 아크 온 시간을 늘리고, 품질 결과를 높이고, 생산 과정에서 더 좋은 부품을 이동하는 데 도움이 될 수 있습니다.
게시 시간: 2020년 2월 2일